First Steps for Drilling a New Well
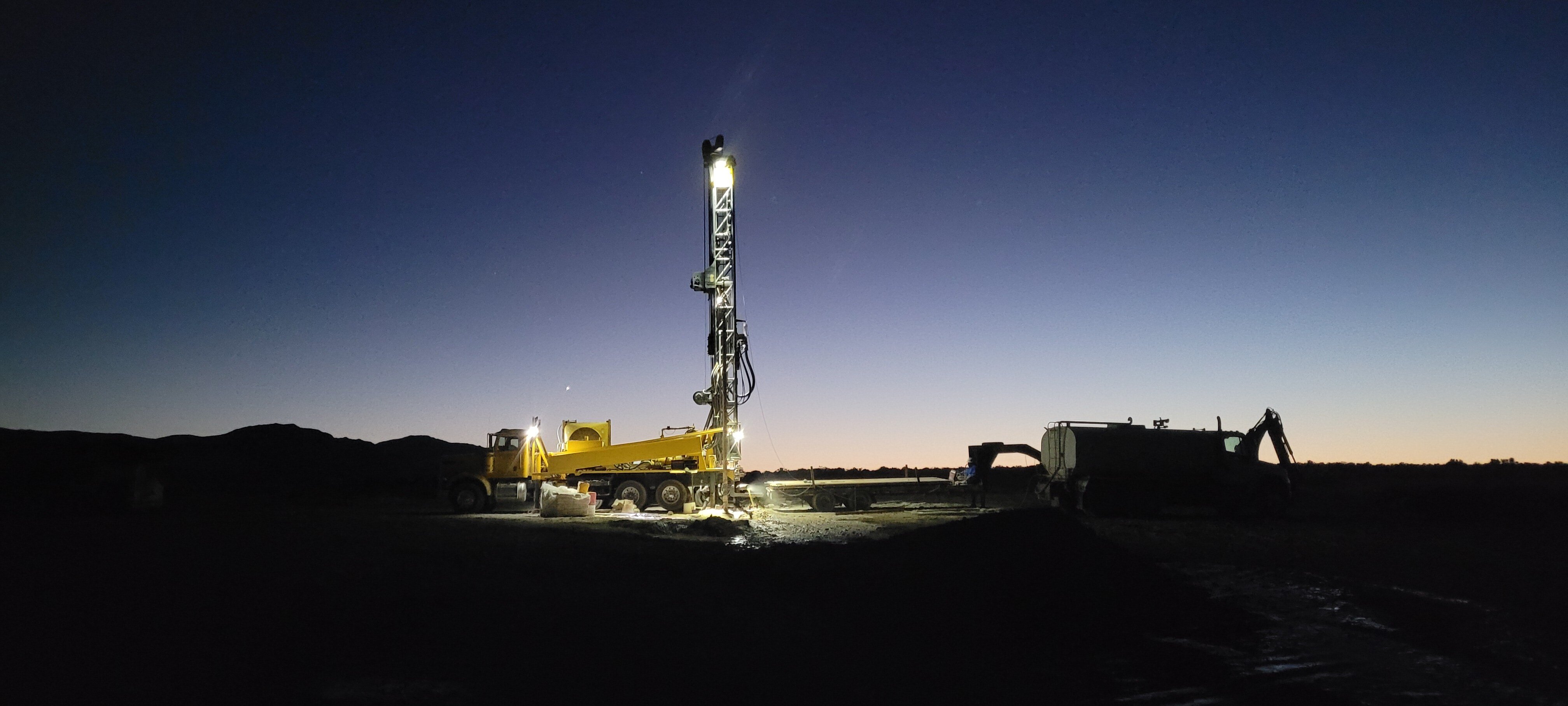
Drilling a new well often is a more involved, and costly project than most people realize. The timing from permitting, engineering, design, drilling, pump system and utilization can extend several months to several years, depending on the project location and requirements. Additionally, the costs of each step can be incrementally more expensive and ultimately lead to being a costly endeavor. While the needs of the water can be easily seen, the challenges faced to put a new well in place, can be intimidating. Here, we are going to look at some of the considerations that need to be evaluated with every project and help provide some insight to help jumpstart your drilling project.
Intended Use
Will this be used for process water, irrigation, or other non-potable application, or will the water be used for drinking water applications? As you can imagine, drinking water wells have to meet more strict standards and all materials used in the well, including the casing, gravel, pumps, and more have to be compliant with the National Sanitation Foundation code NSF-61, meaning it safe to be used in drinking water systems. Additionally, drinking water wells may require additional treatment systems.
Well Location
Where you place the well can be one of the most important factors that impact the costs. Placing a well in hard to get locations, or areas with little access to power, can become very costly. Additionally, tight sites often are very difficulty to get large drilling equipment onto, so costs often will go up if there is limited space at the drilling location.
Permitting
You need to research your local jurisdiction to determine what the requirements are to apply for permits. These can very from state to state, as well as county to county. In Nevada, having appropriate water rights and knowing where your point of diversion is, will be critical for state drilling approval. In California however, permits are issued on the county level, with varying degree of complexity to acquire, based on geographic region.
Electrical Service
As mentioned in well location, power can be a costly part of the drilling project. If locating the well near a large power source isn't possible, being aware of the challenges with moving power is important. Many wells have high horsepower motors with use 240V or even 480V motors and pull high Amps, meaning you need a larger power supply available. Brining new power lines, transformers, or more, is very expensive and the time for implementation can be months or years. In nearly every project, it is less expensive to pump water a further distance then it is to bring power to a more convenient well site.
Materials
Material selection is another critical part of the well design process and can have a drastic impact on cost. The primary material items installed in a well are the casing and the gravel/filter pack that will be used. For casing, materials often are pvc or mild steel for small domestic wells or irrigation wells. If the well is to be used for public drinking water, then High Strength Low Alloy (HSLA) or Stainless Steel are required.
Drilling Types
Mud Rotary - Most common, least expensive method. Good for unstable formations, but requires heavier drilling fluids to be used to keep the borehole open. This can negatively impact well production if not properly cleaned out during well development.
Direct Air - Primary used in hard rock and consolidated formations. this method uses drilling foam and air to grind through extremely hard substrates.
Reverse Circulation - Primary method for high production and municipal supply wells. Reduced amounts of drilling fluids and very clean process. Works in most applications, but not possible in areas with loss circulation or very unstable conditions.
Others - Dual tube, Casing-Advance (Dual Rotatory), Air Hammer, Sonic, Hollow Core, and more. All with unique applications and advantages.
Pump Systems
Final pump systems are difficult to fully determine prior to construction of the well. The reason being is that you need test pumping data on what the well can produce in order to size the final pump & motor. There are primarily 2 types pump systems use water well applications, submersible turbine and vertical turbine pumps. Each have their advantages/disadvantages. Subersible pumps have the motor connected to the pump and is submerged deep into the well, below the water level. These often are common for smaller pumps and domestic applications and have the advantage of being simpler design, however you need to pull the full pump system out to service the motors. A vertical turbine pump however, has the motor above grade with the pump assembly connected via a long shaft down to the pumping water level. This allows for easy access to the motor, but adds the complexity of the long shaft system and more moving parts which could fail. The vertical turbine design, is used for higher flow rates because the motors can be much larger.
These are just a few of the items you should be considering with every new well project. There is no such thing as "cookie cutter" when it comes to drilling projects and each one needs to be reviewed to create the perfect union of performance and cost. The process can be difficult, but our team is here to help. Give Stonehouse Drilling a call and we can help walk you though even the most complex project!